HAND PROTECTION: Guide To Glove Finish
Choosing the right glove dip is crucial for ensuring worker safety and performance in various tasks. Each dip offers unique benefits, making it important to match the glove material to the specific hazards of the job. Nitrile provides superior chemical and abrasion resistance, while polyurethane offers excellent dexterity and durability.
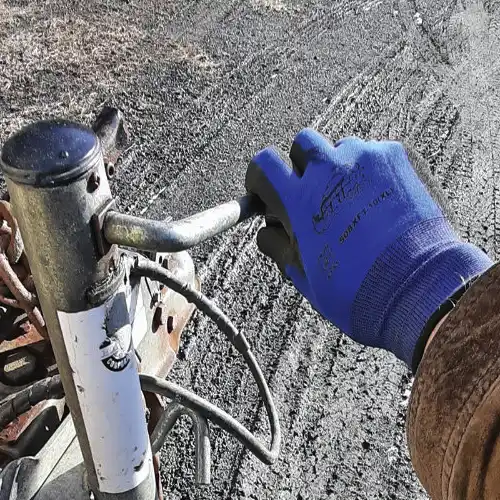
Rubber is known for its strong grip and elasticity, especially in extreme temperatures, and neoprene is ideal for chemical handling due to its resilience to hazardous substances. Lastly, PVC is a cost-effective option for liquid resistance, particularly in petrochemical environments. Below are the charactoristics of each.
Nitrile
Nitrile is a synthetic polymer that is unusually resistant to chemicals, oils and fuels. Due to the superior strength of nitrile, gloves dipped with this polymer also have a higher abrasion resistance compared to other polymers.
Polyurethane
Polyurethane dipped gloves offer a high level of dexterity to the user.
The dip also adheres through the entire glove liner, which prevents flakiness and peeling gloves.
Rubber
Rubber dipped gloves have an inherently strong grip ability and are the most elastic polymer. They perform well under extreme temperatures and do not tear easily. Rubber dipped gloves are not recommended for use with petroleum-based organic solvents.
Neoprene
Neoprene was invented to replace natural rubber in chemical handling situations. It is not susceptible to most hazardous chemicals and can be used safely. It also holds up well to UV light.
PVC
PVC is a low cost, liquid resistant polymer that performs well in petrochemical situations because of good abrasion resistance
and flexibility at low temperatures. Everything you need to know about Glove Dips
Solid
Solid dip resists penetration of liquids and has an excellent dry grip.
Mach Finish
The Mach Finish dip has a higher grip rating, better wear resistance and more protection than solid or foam-dipped gloves.
Dotted
Dotted gloves provide an extra level of grip and extra abrasion resistance when compared to standard dipped gloves, ensuring a better user experience.
Rough Finish
Rough finish gloves have an added level of grip and better wear resistance than solid dipped gloves.
Etched
The grip factor of etched gloves is not reduced by either wet or cold conditions.
Air Injected Foam
While the wear resistance of air-injected foam may not be as high as other finish types, it offers enhanced dexterity and outstanding grip in wet/oily situations.
Engineered Foam
When compared to other foam dipped gloves, engineered foam has an increased level of wear resistance, good dexterity and a lower cost.
New Foam Technology
With a high degree of dexterity and grip in wet or oily conditions, New Foam Technology dipped gloves offer the user a comfortable, effective option.
Xtreme Foam Technology
A performance blended foam dip, Xtreme Foam Technology offers excellent dexterity and grip in wet or oily conditions.
Helmet Maintenance and Inspection
How to Choose the Best Construction Helmet for Your Team
What is the difference between a bump cap and a helmet?
Print the chart at 100% and place your hand over the graphic to choose the right size glove. Contact us if you would like a sample glove for your employees.
For a complete in-depth understanding of which glove to choose for your industry click or download >>>
Easily identify a best selling glove solution based on the common function and protection features necessary to get the job done in industrial applications.